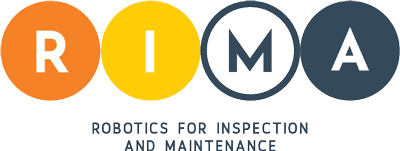
Period: 15. 09. 2021 – 29. 10. 2022
Funding SOURCE: Horizon 2020
TOTAL BUDGET:
PROJECT COORDINATOR: FOKUS TECH d.o.o.
GEMMA COORDINATOR: dr. David Podgorelec
PROJECT PARTNERS:
- FOKUS TECH d.o.o., Celje, Slovenia (with UM FERI as a subcontractor),
- ALTPRO d.o.o., Zagreb, Croatia.
Project website: rimanetwork.eu
LINKEDIN: /
Autonomous Mobile Robots for Inspection of Railway Lines
Abstract:
Railway safety is threatened by landslides, falling rocks and trees, floods, collapses of rail lines and load-bearing structures, torrents, and other hazards. Unlike the SMART2 project, where statically installed LiDAR sensors were used to monitor dangerous areas at level crossings of railway and roads, much wider open sections of railways require a new concept for inspection. InspectRAIL thus introduces inspection by autonomous mobile robots, which move through dangerous places along the railway lines on steel cables stretched between the catenary masts and operate in all weather conditions. The robots are equipped with LiDAR sensors and video cameras which inspect the railway tracks. The acquired data is automatically processed and sent to the Intelligent Control System (ICS), signaling system, traffic control, and maintenance centre for further actions. As movement requires higher frame rates than statically mounted sensors, a contemporary Ouster OS1 LiDAR sensor was chosen.
GeMMA was responsible for developing the ICS, where several challenges had to be addressed. Detection of rails was initially designed on the reflectivity measurements performed by the utilized sensor, but this solution was not stable enough in varying weather condition, so the solution was then completely designed on geometric data only. In normal conditions, the rails are about 15 cm above their surroundings, but we had first to align the point cloud due to sagging of the wires and the robot tilt due to wind. An external inertial measuring unit (IMU) was used for this task, which requires synchronization with LIDAR among all. The obstacle detection is then performed in a simple manner. LiDAR points detected below the top of the sleeper (TOS) plane in the section of the railway track correspond to lack of the ballast and must be reported as a potential danger. The second dangerous section is above the top of rail (TOR), where no obstacle should be detected. Besides detecting the obstacles and sending alerts, ICS must also display the mileage which represents the position of the robot relative to the reference rail system. The mileage is calculated from the data of the encoders of the drive motors and the radio frequency identification (RFID) tags on the poles of the overhead contact line.
The Camera view of the ICS with alert indicator due to detected obstacles.
The robot (in the yellow circle) with LiDAR and camera during the detection of obstacles in the test area (photo: archive of FOKUS TECH d.o.o.).
![]() | ![]() |
The LiDAR view of the ICS with detected rails (yellow) and obstacles (red) in the point cloud (photo: archive of FOKUS TECH d.o.o.). | Besides the obstacles above the rails, the system must also detect holes in the track ballast (photo: archive of FOKUS TECH d.o.o.). |
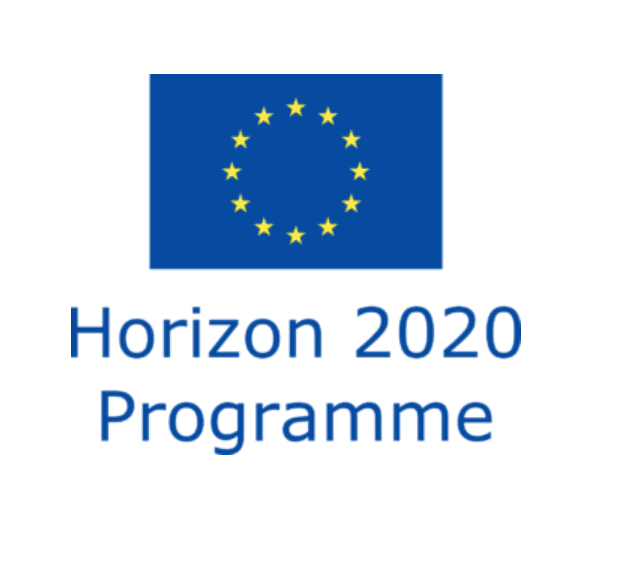